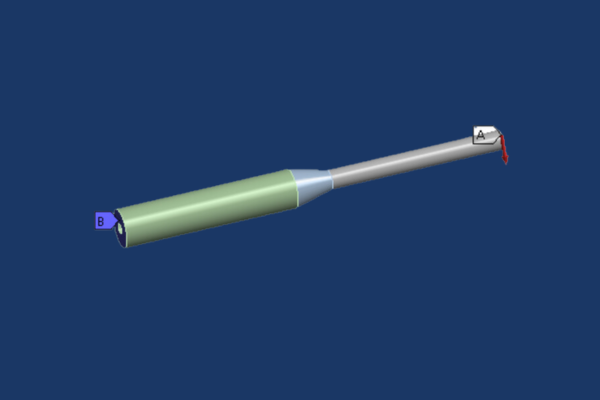
Ansys nCode DesignLife Training
Ansys nCode DesignLife
Two-Day CourseThe objective of this course is for attendees to develop a strong expertise in the use of Ansys nCode DesignLife for durability and fatigue analysis. The course also demonstrates several examples of setting up and solving DesignLife simulation within the native Mechanical GUI using the “Mechanical Embedded DesignLife” ACT extension. The course covers a broad array of topics focusing on stress life for high cycle fatigue to strain life for low cycle fatigue studies, duty cycle vibration fatigue to simulate virtual shaker table test, as well as seam weld fatigue on thin plate weldments meshed with shell finite elements to solid welds on thicker tubular structures.
The 2-day course includes training materials from Ansys, Inc. that delivers nine instructor-led lectures and ten workshops, as well as DRD Supplementary workshops that demonstrates additionally eight practical examples of fatigue covering different applications.
Prerequisites for this course are DRD’s Introduction to Ansys Mechanical course, and/or some level of proficiency with the Ansys Mechanical user interface.
Lecture 1: Introduction to CAE Fatigue
The goal of this workshop is to examine how Ansys nCode DesignLife interacts with Ansys Mechanical on the Workbench platform.
Lecture 2: HBM nCode (Standalone) Interface
Workshop 2.1: Constant Amplitude SN Fatigue Analysis Using HBM nCode Interface
The goal of this workshop is to examine how Ansys nCode DesignLife interacts with Ansys Mechanical on the Workbench platform.
Lecture 3: Workbench Integrated Interface
Workshop 3.1: Constant Amplitude SN Fatigue Analysis Using Workbench Integrated System
Workshop 3.2: Time Series SN Fatigue Analysis Using Workbench Integrated System
Lecture 4: Stress Life Fatigue Analysis Using Ansys nCode DesignLife
Workshop 4.1: Time Step SN Fatigue Analysis
The goal of this workshop is to import FE model into Ansys nCode DesignLife, review the FE results and selectively choose subsets of the full model to run fatigue calculations.
Workshop 4.2: Stress Life Fatigue Analysis Using Add-On
Lecture 5: Strain Life Fatigue Analysis Using Ansys nCode DesignLife
Workshop5.1: Constant Amplitude EN Analysis with Mean Stress Correction
The goal of this workshop is to learn how to modify material mapping.
Workshop 5.2: Fatigue Evaluation of Wind Turbine Using Ansys nCode DesignLife
Workshop 5.3: Strain Life Fatigue Analysis Using Add-On
DRD Supplementary Workshops
Workshop 1: Fatigue Analysis of a Simple Shaft under Combined Bending and Torsion Loads
The goal of this workshop is to calculate the fatigue life of the drive shaft using Ansys nCode DesignLife time series loading. The stresses from unit bending and torsion load cases in Mechanical are paired with corresponding measured load histories to generate stress history that allows DesignLife to perform fatigue calculations using Rainflow Cycle Counting and damage assessment using Miner’s Rule.
Workshop 2: Fatigue Life Prediction for a Telecommunication Rack Subjected to El Centro Earthquake Seismic Loads
The goal of this workshop is to perform a full transient dynamic analysis within Ansys Mechanical and use the time history results to determine life of cabinet from this transient excitation in Ansys nCode DesignLife.
Workshop 3: Low Cycle Fatigue (LCF) using Nonlinear Stresses and Strains
The goal of this workshop is to evaluate strain life fatigue using nonlinear stresses and strains from Ansys Mechanical. The nonlinear material characteristic is defined using the Multilinear Kinematic Hardening plasticity.
Workshop 4: Fatigue Analysis of a Trailer Spindle Subjected to Multiple Time Series Load Histories
The goal of this workshop is to evaluate fatigue life of a trailer spindle subjected to duty cycle loading within Ansys Mechanical using Mechanical Embedded DesignLife ACT extension.
Workshop 5: Virtual Random Vibration Shaker Table Test of a Marine Alternator Bracket
The goal of this workshop is to perform a vibration fatigue analysis using sequential multi-axis (3 axis) excitation of a marine alternator bracket to mimic a virtual shaker table test (VSTT) by using duty cycle loading in Ansys nCode DesignLife.
Workshop 6: Seam Weld Fatigue Analysis on a T-Joint Welded Assembly Meshed with Shell Finite Elements
The goal of this workshop is to perform a seam weld fatigue analysis in Ansys nCode DesignLife using the shell weld finite element model results from Ansys Mechanical.
Workshop 7: Seam Weld Fatigue Analysis on a T-Joint Welded Assembly Meshed with Shell Finite Elements using the Mechanical Embedded
DesignLife ACT Extension
The goal of this workshop is to perform a seam weld fatigue analysis within Mechanical using the “MechanicalEmbeddedDesignLife” ACT extension.
Workshop 8: Seam Weld Fatigue Analysis on a T-Joint Welded Assembly Meshed with Solid Finite Elements
The goal of this workshop is to perform a seam weld fatigue analysis in Ansys nCode DesignLife using the solid weld finite element model results from Ansys Mechanical.