Introduction to Ansys CFD (Fluent)
two-day courseThis course provides an introduction to conducting CFD simulations in Ansys CFD.
The course devotes little time to CFD theory and focuses on practical use of the software through both lectures and workshops that demonstrate practical problems. Workshops build in difficulty throughout the course and develop skills in setup, solving, and postprocessing models in Fluent.
Early workshops create geometry from scratch or import CAD geometry as starting points. This allows students to build skills with meshing and geometry preparation. Latter workshops utilize pre-generated mesh files allowing for more complex problems to be undertaken during class time.
DRD encourages the students to be ready to discuss their application for Fluent with the instructor so that we can best tailor the training to each student.
DRD conducts this course over two days. Students will receive all training materials to take home and reference later.
Chapter 1 – SpaceClaim User Interface, Basic Operations, and Creating Geometry
Workshop 1.1 – SpaceClaim Basics
In this workshop we introduce Ansys SpaceClaim and use it to extract a fluid volume from a mixing tee.
Workshop 1.2 – Geometry Repair using SpaceClaim
This workshop introduces the use of automated repair tools in SpaceClaim.
Workshop 1.3 – Creating a Mixing Tee from Scratch
This workshop demonstrates creating geometry from Scratch in SpaceClaim.
Workshop 1.4 – Creating Named Selections and Bodies of Influence in SpaceClaim
This workshop introduces creation of named selections and bodies of influence. Shared topology considerations for bodies of influence are also discussed.
Chapter 2 – CFD Overview
Workshop 2 – Mixing Hot and Cold Streams in a Mixing Tee
This workshop covers the creation of a model in which two air streams at different temperatures are mixed together. The mixing uniformity is analyzed.
Chapter 3 – Watertight Geometry Workflow Overview and Surface Meshing
Workshop 3 – Meshing of a Static Mixing Device
Chapter 4 – Geometry Description and Volume Meshing
Workshop 4 – Meshing of a PCB and Heatsink
This workshop covers meshing of a heat producing electrical component on a circuit board. The board, component, heatsink, and surrounding air are meshed in preparation for solving.
Chapter 5 – Solution Mode User Interface
Workshop 5 – Flow Distribution in an Air Manifold
This workshop demonstrates how to conduct a simple flow analysis in Fluent. Relative flow rates between the outlets are also examined.
Chapter 6 – Physics Tab
Workshop 6 – Meshing and Solving Using Zero Thickness Baffles
A duct with turning vanes is meshed in Fluent Meshing and solved. Proper meshing of zero thickness baffles is demonstrated.
Chapter 7 – Results Tab
Workshop 7 – Flow Over Heated Obstacles
This workshop introduces heat transfer via wall boundary conditions and utilizes symmetry to speed up computation of the solution.
Chapter 8 – Solution Tab
Workshop 8 – Solver Options and Settings
The mixing tee model is reexamined using various solver settings to see how they affect convergence behavior and result quantities.
Chapter 9 – Best Practices
Workshop 9 – Turbulent Flow Past a Backward Facing Step
Flow separation on a backward facing step is analyzed. The effect of including an accurate inlet velocity profile is also explored.
Chapter 10 – Turbulence
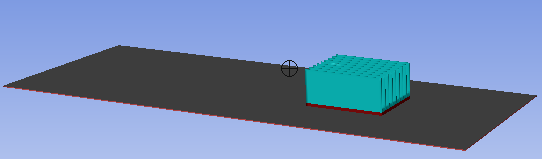
This workshop covers the conjugate heat transfer analysis of a heated chip and heatsink undergoing natural convection. Surface-to-surface radiation is also examined.