Fluids Simulation Tools
Overcome Fluid Problems Quickly and Accurately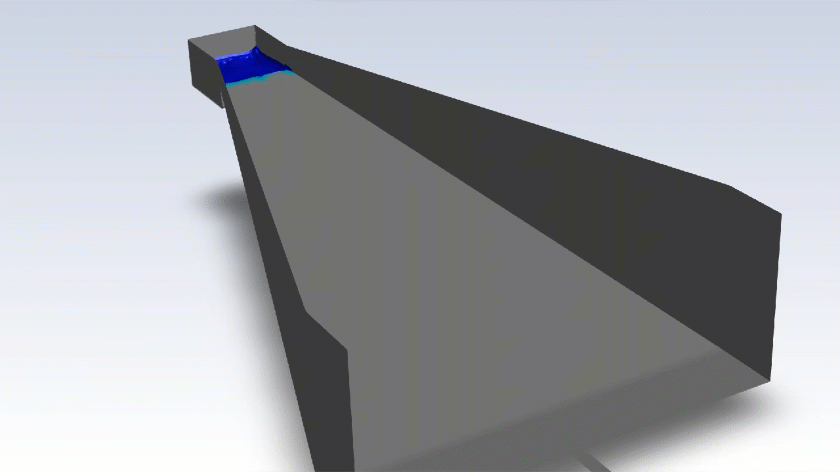
Engineering flows can be complex and physical testing is costly and can only provide so much fidelity. With a fully equipped CFD simulation suite, you can minimize required design cycles, trim development costs, and accelerate time-to-market. Headlined with the flagship Ansys Fluent, the leading CFD software for multiphase flow and combustion, the Ansys CFD software suite includes a variety of tools from turbomachinery (Ansys CFX) to granular flows and DEM (Ansys Rocky) to electronics cooling (Ansys Icepak) to handle every application.
Streamline fluid analysis with precision using Ansys Computational Fluid Dynamics (CFD). This robust software suite provides a comprehensive set of tools including world class meshing technology, multiphase and multispecies analysis, discrete element modeling, and more. Ansys Mosaic meshing technology, embedded in a task-based workflow, allows seamless connection between multiple element types all while reducing the amount of engineering time required to achieve a high quality and high efficiency mesh. Ansys Fluent also integrates natively with Ansys FEA and electromagnetics tools bringing you a true Multiphysics simulation platform. As the Ansys CFD software suite is offered in three increasing levels of features, DRD technology experts will work with you to ensure you have the right software capabilities and training you need to succeed in simulating your toughest problems.
Drive better design faster with comprehensive fluid analysis tools from Ansys and DRD Technology.
Solutions to Your Toughest Fluid Challenges
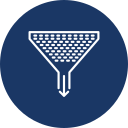
Bulk Material Handling
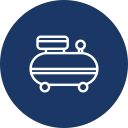
Turbomachinery
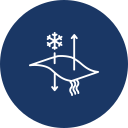
Electronics Cooling
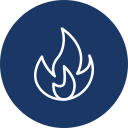
Combustion
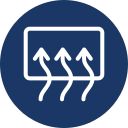
Ice Formation
Best-In-Class Meshing Technology for Fluid Simulations
Ansys Fluent provides a guided workflow with a step-by-step process of simple, intuitive inputs, while behind the scenes, Fluent Meshing uses built-in intelligence and automation to create a high-quality CFD mesh. Ansys Fluent’s patented meshing technology uses an innovative poly-hexcore meshing algorithm, tools for high-quality boundary layer mesh generation, and parallel meshing. This workflow enables all users to complete all stages of a CFD simulation, from meshing through to post-processing, entirely within the same software session and in the same single-window user environment. Referred to as Mosaic Technology, it results in the most accurate and efficient mesh in the industry with often far fewer nodes and elements than similar products.
Mosaic Meshing Technology Advantages:
- Mosaic technology enables polyhedral connections between disparate mesh types as shown in the images below. The mesh is conformally connected between polygonal prisms on the boundary to bulk Cartesian aligned hexahedral cells.
- Hex dominant allows for faster meshing and a better-quality volume mesh which often produces a solve time reduction of 30-50%.
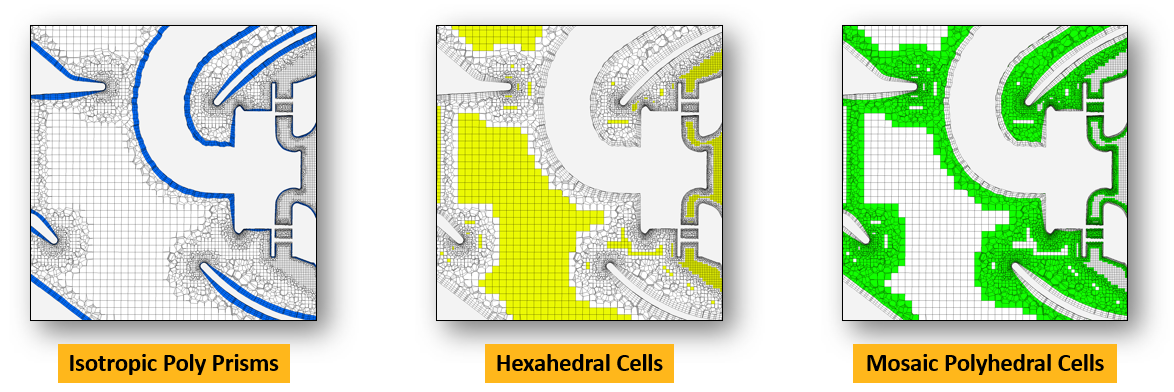
More simulation capabilities, less execution time
Ansys High-Performance Computing Solutions
As product sophistication increases, your simulation needs evolve. To maximize productivity, you need high-fidelity models that incorporate multiple physics across entire systems. This requires more computing power coupled with software that can truly leverage your hardware investment. With Ansys High-Performance Computing (HPC) solutions, you can select the level of computing power you need to support your parallel processing, distributed solving, parametric analysis, or multiphase model requirements so you can get to market faster with a more reliable product.
To accelerate your Ansys Fluent fluid simulations, Ansys HPC licenses can be used to scale your solutions on your CPU cores. In addition, a GPU specific solver has been added to Ansys CFD for incredible performance improvements. For more information and a validation study on this GPU solver, you can download a white paper here.
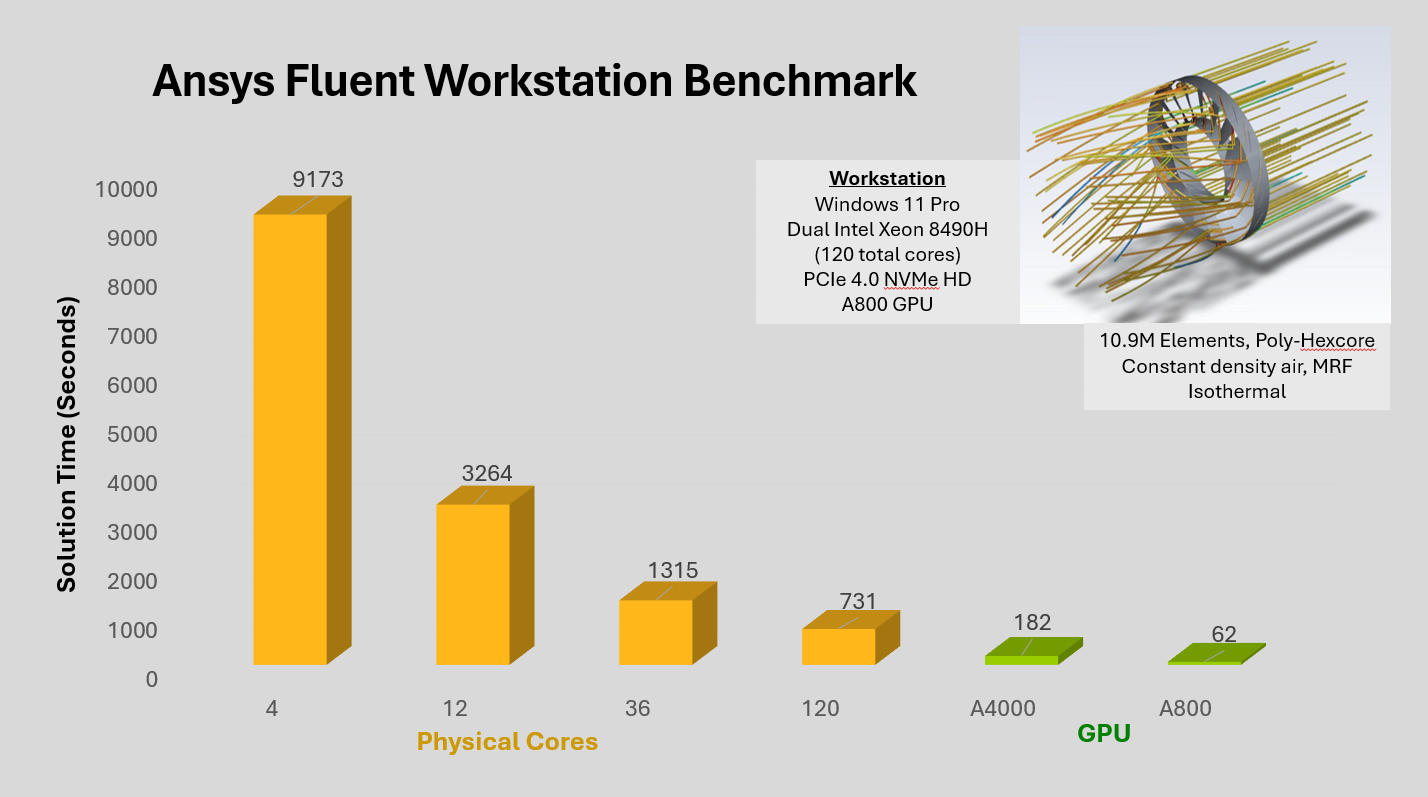
Application Examples
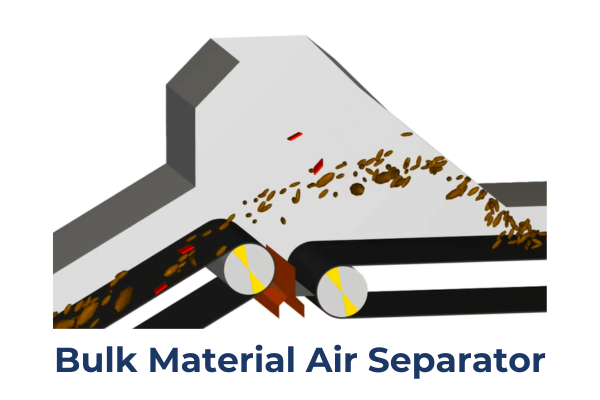
Air Knife Used to Separate Bulk Materials of Different Densities
This simulation is of an air knife used to separate bulk material of different densities. The conveyor contains a variety of materials in different sizes, shapes, and densities such as rock, paper, aluminum cans, etc. The objective of the simulation is to separate the lightweight paper from the solids and identify areas where material will collect or get trapped. Baffles and material diverters can be quickly added and adjusted to adjust performance. Wear on the equipment can also be identified.
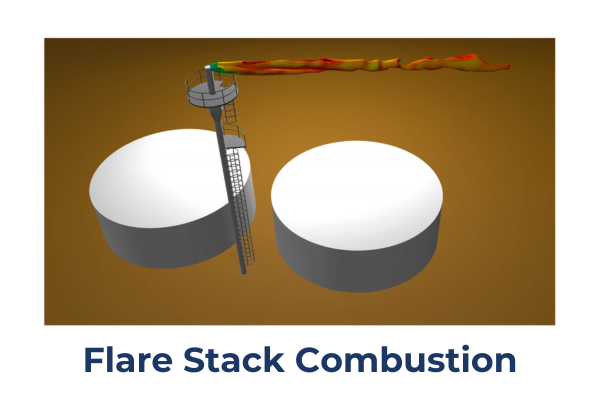
Flare Stack Combustion
Methane is released from the end of flare stack and burned under moderate wind conditions (25 MPH). This animation shows the location of CO at 5000 PPM colored by the gas temperature. The gas ignites a short distance downstream of the flare, thus the temperature of the gas is highest away from the flare tip, and eventually all products are combusted.
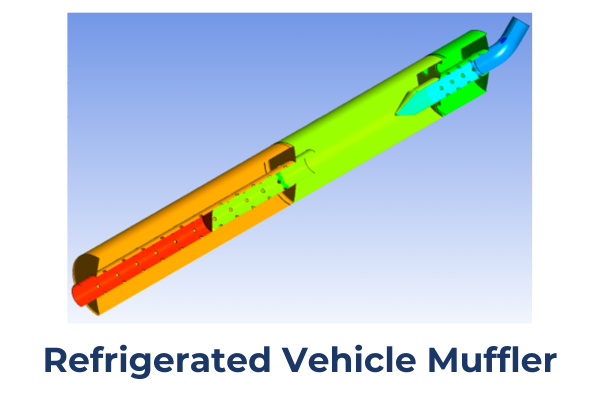
Muffler for Refrigerated Transport Vehicles
This figure shows geometry simulated by Nelson Global to optimize their muffler performance. The baffles and internal geometry were modified and simulated repeatedly to produce the desired silencing effect. Good correlation was observed between their simulation data and the final design that was experimentally measured. This modified design came to market significantly faster for their end customer through the use of CFD simulation.
Design. Simulate. Succeed.
Comprehensive Fluids Software Training
At DRD technology our goal is to arm you with the skills you need to conquer your most difficult simulation challenges. We offer many training opportunities for you to get the training experience you need to succeed. This includes introductory courses for new users, and more advanced courses for those seeking to further develop their knowledge.
Introduction to Ansys CFD
Introduction to Ansys Rocky
Introduction to Ansys CFX
Workbench Meshing for Ansys Fluent
Additional Resources
Enhance your fluids simulation skills with our in-depth resources.