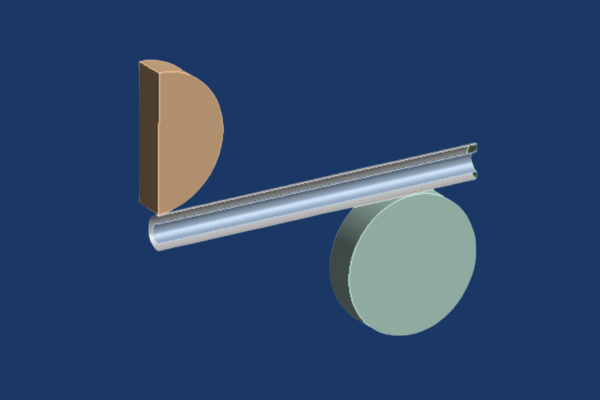
Ansys Workbench LS-DYNA
Ansys Workbench LS-DYNA
Two-day courseThe objective of this course is for attendees to develop expertise in the use of Ansys Mechanical for explicit dynamic analysis using Ansys LS-DYNA. Ansys LS-DYNA has a wide variety of applications in many industries such full car crash testing in the automotive industry, windshield bird strike simulation in the aerospace industry, cell phone drop test simulation in consumer electronics, and deep drawing, hydroforming, and superplastic forming simulation in advanced manufacturing.
This 2-day course includes ten workshops and nine instructor-led lectures to cover basic explicit dynamics theory and applications.
Prerequisites for this course are DRD’s Introduction to Ansys Mechanical course and/or proficiency with the Ansys Mechanical user interface. This is a challenging course for proficient users.
Course Requirements:
Ansys Version used to create course content: 2021 R1
Ansys Version DRD instructor will use for the course: 2023 R1
Ansys Version(s) students may use for the course: 2023 R1
Registration for all classes will close 5 business days in advance of the class date.
Learn more: Agenda + Course Description
Module 1 - Explicit Theory and Workbench LS-DYNA
Workshop 1.1 – Taylor Impact
The goal of this workshop is for students to become familiar with the Ansys LS-DYNA workflow and learn how to perform an impact test simulation. In this Taylor impact test, a cylinder made of elastic-plastic steel hits a rigid wall with an initial velocity and the goal is to determine the contact interaction forces and energy exchange from this impact simulation.
Module 2 - Solution Setup, Boundary Conditions, Rigid Bodies
Workshop 2.1 – Rotary Draw Bending
This workshop involves bending a “Profile” by 70 degrees using a rigid tool. In this example, the rigid “Rotating Die” and “Clamp Die” will rotate about the Y axis dragging the “Profile” along as it slides along the stationary Mandrel. The “Pressure Die” translates axially along the Z axis while it maintains pressure against the “Profile” as it’s formed over the circular trajectory of the “Rotating Die”.
Workshop 2.2 – Drop Test Wizard
This workshop demonstrates the use of the Drop Test Wizard built into Ansys Mechanical to set up and simulate dropping a circuit board from a height of 1 meter.
Module 3 - LS-DYNA Results and Postprocessing
Workshop 3.1 – Postprocessing with LS-PrePost
This workshop navigates into the LS-PrePost environment to review some of the postprocessing capabilities with LS-PrePost interface, which is included with Ansys LS-DYNA.
Module 4 - Connections
Workshop 4.1 – Impact on Tubes
In this workshop two nested (concentric tubes) are struck by an impactor approaching at an initial velocity of 30 meters per second. The tubes are connected at outer ends through caps and supported by rotatable cylinder.
Module 5 - Quasi-static Analysis and Result Verification
Workshop 5.1 – Quasi-static
This workshop utilizes the tube impact test example that involves dropping a tool to hit the tubes. In this workshop; however, we conduct a Quasi-static analysis to study the load from a hydraulic cylinder. The speed of the cylinder is based on the hydraulic pump and the controls system and can take a few seconds to run. It would take a long time to run this in the physical time frame, but the concept of Quasi-static simulation can help accelerate it.
Module 6 - Engineering Data and Material Models
Module 7 - Meshing
Workshop 7.1 – Meshing
This workshop gives users experience with generating a uniform mesh for both solids and shells with a specific number of element divisions on curved geometry.
Module 8 - Element Formulations
Workshop 8.1 – Drop Test
In this workshop we perform a drop test simulation in which we drop a mobile phone from a height of 1.5 meters.
Workshop 8.2 – Bird Strike
In this workshop an impact simulation is performed in order to study the effect of a bird strike on an aircraft wing section. The bird is modeled using Smooth Particle Hydrodynamics (SPH).
Module 9 - LS-DYNA Keywords
Workshop 9.1 – Crimping Process
In this workshop, a “Crimper” moves a prescribed velocity and deforms the “Crimp” to create a shaped connection between the bundled wires and “Crimp”.