In an increasingly competitive landscape, companies invest heavily in reducing costs and time to market. Traditional techniques of modeling, testing, and prototyping are no longer viable. Using computer-aided engineering (CAE), companies can mimic physical drop tests and impact tests at a fraction of the cost, saving millions of dollars. With Ansys LS-DYNA, companies can simulate material failure, component deformation, and energy absorption related to various test standards and specs.When was the last time you had the harrowing experience of dropping your expensive smartphone on the road while loading your groceries into your car, ending up with a cracked screen? Or perhaps you damaged your smartwatch by hitting it against a doorknob? Consumer electronics are highly susceptible to damage from accidents and shipping mishaps, leading to costly replacements and customer dissatisfaction. Companies are constantly exploring innovative ways to improve product design for better sustainability and durability against impacts and drops.
The Widespread Application of Drop and Impact Testing
The application of drop testing extends beyond consumer electronics. It includes:
- Automotive Industry: Vehicle front-end collision with a concrete barrier.
- Aviation Industry: Bird strikes on the leading edge of an aircraft.
- Transportation Sector: Packages dropped during transit.
- Military Applications: Impact of kinetic energy projectiles like bullets piercing armor plates.
Using our Ansys LS-DYNA explicit simulation capabilities, users are able to simulate drop tests and impact tests much more comprehensively and efficiently.
What are the Advantages of Running Computer Aided Simulation?
In the ever increasing cutthroat competitive landscape companies are heavily invested in ways to reduce cost and time to market and the traditional technique of modeling, testing and prototyping is not a viable option anymore. Using computer-aided engineering (CAE) companies are able to mimic these physical drop tests and impact tests which are otherwise very expensive and time consuming at a fraction of the cost which can save companies millions of dollars. Using our Ansys LS-DYNA tool, companies are able to simulate drop tests to simulate material failure, component deformation, energy absorption related to various test standards and specs. With our tool creating a virtual prototype is fast and easy and facilitates easy design iteration process that yields fast and reliable results and the ROI on the software investment is more than justified when comparing this to expensive physical tests.
Drop Test and Impact Test Simulations with Ansys LS-DYNA
Cell Phone Drop Test
This simulation involves dropping a generic mobile phone from a height to impact with the ground.
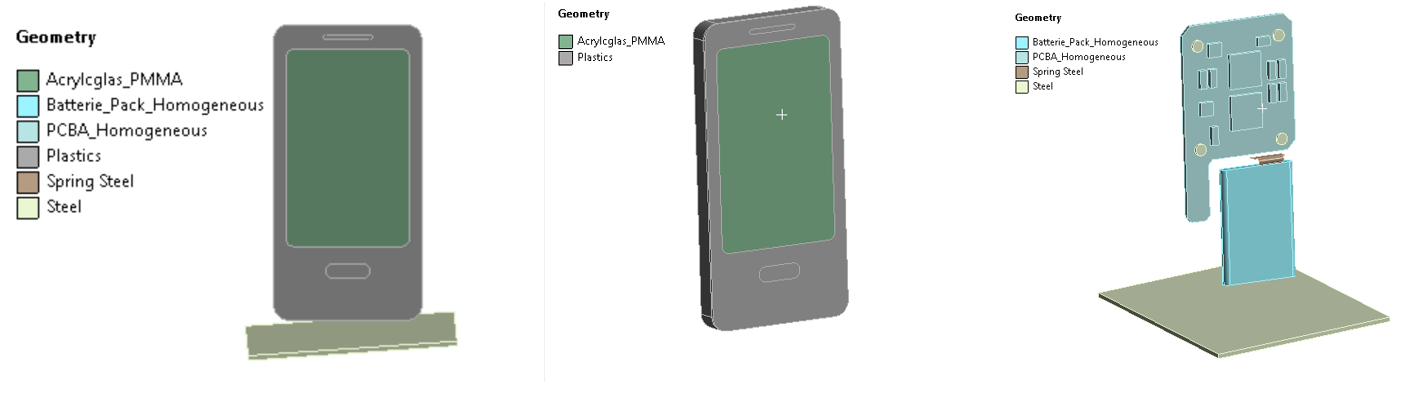
The mesh count was well under 30k elements and CFL timestep was plotted to ensure we could use small amount of mass scaling to expedite the solve if needed as shown below.

The animation below shows the result from the cell impacting the ground.
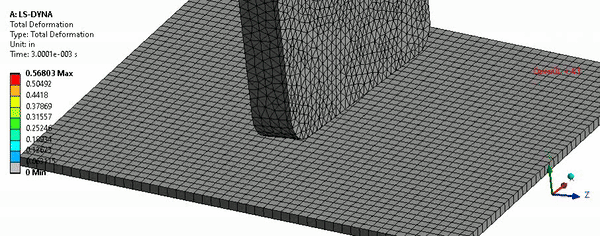
The animation above reveals the battery pack separating from the lower housing due to frictional sliding which attributes to the negative contact energy as observed on the plot below for energy summary.
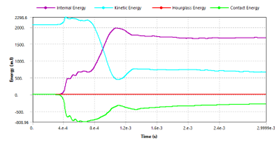
In addition to stresses and deformation on the various objects we can also gather useful information on contact force transmitted between the device and ground as shown below.
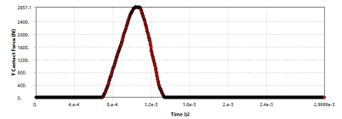
Bird strike on the leading edge of an aircraft
Bird strikes are fairly common occurrence that can happen when the aircraft is flying at low altitudes especially in situations of take off and landing. The bird strikes can be quite catastrophic if the bird strikes the windshield of an aircraft or gets sucked into the engine or as in this case hits the leading edge of the airfoil of the aircraft that can cause structural damage.
The aviation industry is heavily focused on not only ensuring that such occurrences do not occur but in the circumstances, they do occur that the structural integrity of the aircraft is not compromised.
In this example the airfoil which is the structural part (“Lagrangian” body) is comprised of a Multibody part comprising of an outer skin and four interior stiffeners inside. The airfoil material is defined as “Aluminum” and is modeled in Ansys LS-DYNA using the Johnson Cook strength material model. The bird is idealized as an “ellipsoid” shape and simulated using Smooth Particle Hydrodynamics (SPH) in LS-DYNA. The material assigned to the bird is “water” which includes an equation of state and tensile pressure failure set to 0 Pa to easily allow the body of the bird to disintegrate on impact. The graphic below explains the various aspects of the geometry and material setup.
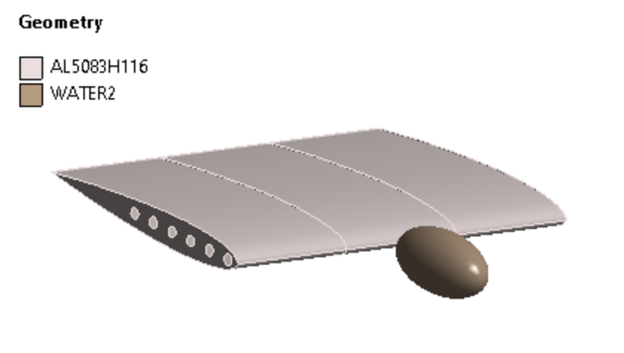
Provided below is a closeup view of the finite element mesh. The mesh reveals the airfoil which is the “Lagrangian” part and the bird is defined as “SPH” part viewed as particle mesh.
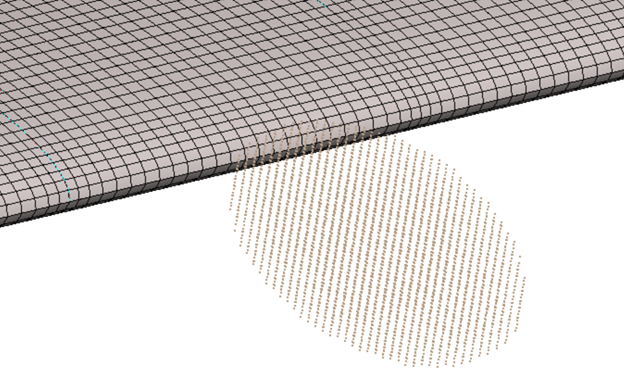
The bird is designed to impact the aircraft approaching at approximately 900 km/hr to mimic the speed of the aircraft at time of impact. Provided below are snapshots of the plastic strain and deformation showing extensive damage to the airfoil structure post impact.
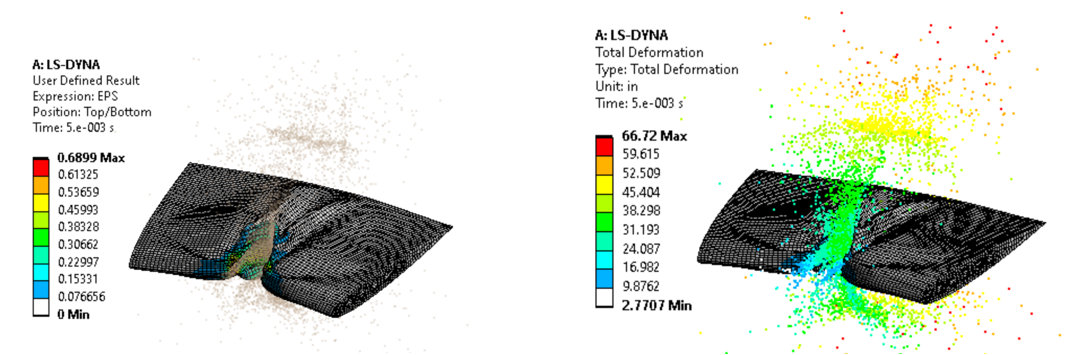
Provided below is an animation of the bird strike simulation.
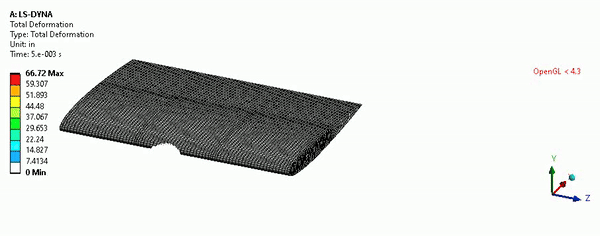
Maritime collision
The rapid increase in maritime traffic makes risk of collision higher in areas of high traffic places. The consequences of ship collision can be quite catastrophic which can be detrimental to not only the environment but also put the ships crew under risk and hence a huge amount of emphasis is put into consideration in the design stage of the ship.
The graphic below shows the collision between a tanker and ferry and this impact simulation was solved using Ansys LS-DYNA.
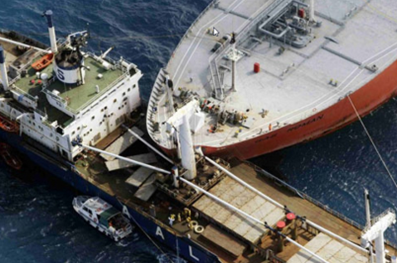
The tanker and ferry were defined as “Lagrangian” parts; Johnson Cook material model was used to define the elastic-plastic behavior and the plastic strain failure was used to simulate failure. The graphics below show the finite element mesh for the simplified model taken into consideration and material law used.
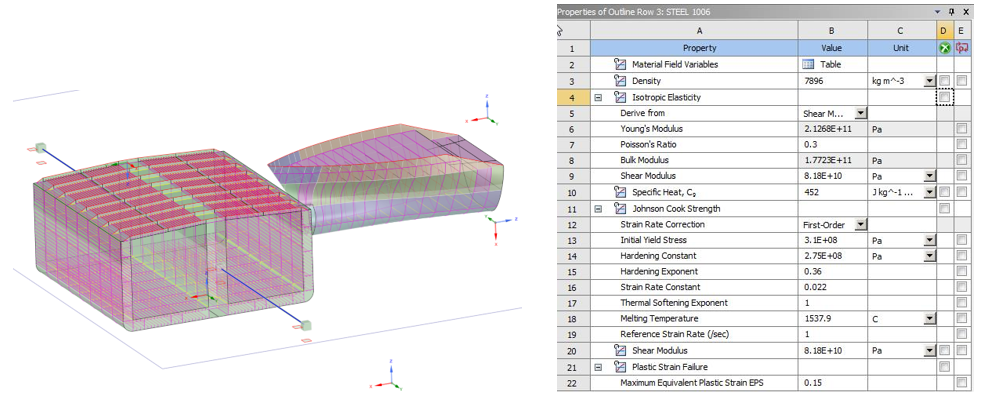
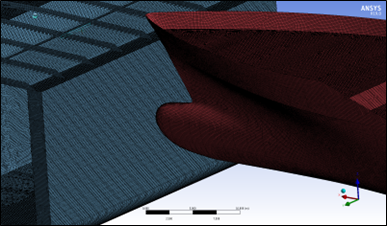
The initial velocity of 3 m/s was applied to the cruise ship and contact was defined as single surface contact to ensure self-impact.
Provided below are graphics of the plastic deformation showing significant damage on the hull of the fuel tanker.
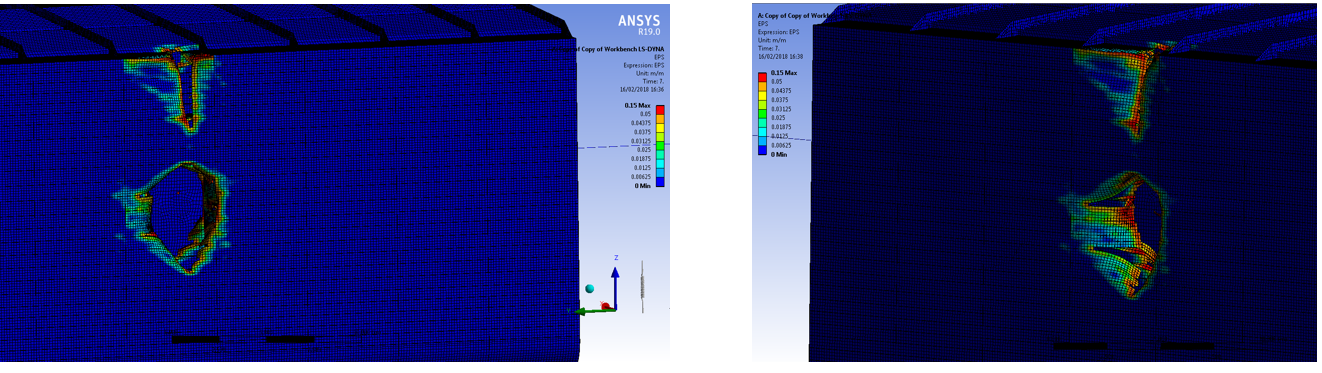
The animation below captures the simulation of the collision between the tanker and ferry.
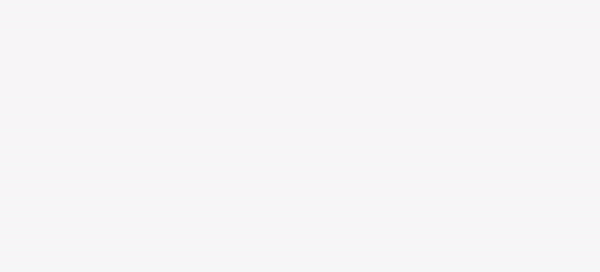
The applications above demonstrate the power behind virtual prototyping to simulate any sort of drop test or impact test and Ansys LS-DYNA is able to calibrate test results very closely.
Explore the Full Potential of Ansys LS-DYNA
The applications above demonstrate the power of virtual prototyping to simulate various drop and impact tests. Ansys LS-DYNA can calibrate test results very closely, offering significant advantages over traditional testing methods.
Don’t Miss Our Webinar on Advanced Simulation Techniques! Watch now!