Transferring Deformed Geometry Between Ansys Applications
Often there is a need to export the deformed geometry from Ansys Mechanical. Possibly to a 3D printer to show to customers, or maybe a new CAD geometry file is needed that can be used for drawings or further design evaluation. Ansys Mechanical offers two options for users for doing this task.
Exporting STL (Standard Tessellation Language) files from the deformed results is one option. The STL file may be opened within Ansys Discovery and reverse engineered to create deformed solid geometry from the STL facets.
I have posted a YouTube video that demonstrates this technique. In the video, I have a rubber cushion that is compressed between two metal plates as shown. The rubber geometry gets deformed and the goal here is to export the deformed faceted geometry and create smooth solid geometry from that.
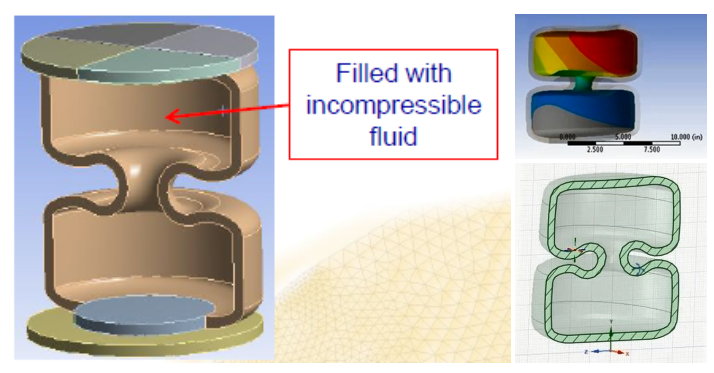
Ansys Mechanical can also export a deformed geometry in a proprietary PMDB (Part Manager Database) format which can be opened up within Ansys Discovery and modified further, or it can simply be opened up within Mechanical for further analysis.
I have also posted a YouTube video that shows how to work with this PMDB file format. In this video, we transfer the deformed geometry shown above from a previously solved FEA and then link its Solution cell to the Model cell of a new Static Structural block.