Discovering New Possibilities With Ansys Discovery (and is SpaceClaim going away??)
If you’ve paid attention to new and emerging technologies in the world of simulation, you may be wondering, “What’s all this hype about Ansys Discovery?” In this blog, we will help answer this question by discussing some of the key features in Discovery, as well as what the future holds for current SpaceClaim users.
Is Discovery Modeling replacing SpaceClaim?
The older SpaceClaim interface has joined DesignModeler as a maintenance mode product in 2023R2. This means the SpaceClaim GUI will continue to be available, and Ansys will continue to perform major bug fixes. However, all new modeling capabilities are being developed within the Ansys Discovery Modeling interface.
How does the new license structure work?
The Discovery Modeling license give you access to all 3 of Ansys’ modeling applications:
- Discovery Modeling (Simulation comes with Discovery Simulation license)
- SpaceClaim
- DesignModeler
Discovery Modeling and SpaceClaim can also be accessed through Enterprise or PrepPost bundles
SpaceClaim and DesignModeler standalone licenses have been discontinued
Benefits of Switching to Discovery Modeling
I already use SpaceClaim, why should I consider learning Discovery Modeling?
If you are a SpaceClaim user, you may be wondering if it is worth your while to switch to something new. Before we dive into new features of the Discovery Modeling package, let’s talk about what this transition actually looks like:
- With Discovery Modeling license, you can simply open your existing SpaceClaim geometry in Discovery from the workbench page and pick up your projects right where you left off.
If you’re starting a new model from scratch, Discovery continues to support direct import of major external CAD formats.
- Discovery gives you access to the same features you love from SpaceClaim with a new and improved UI. Ie, Familiar tools with new and improved functionality.
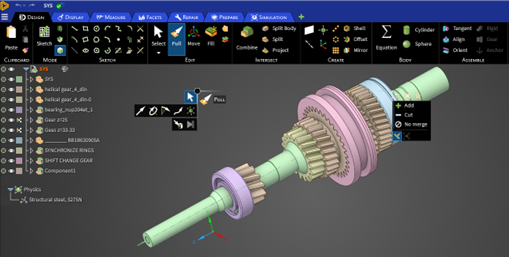
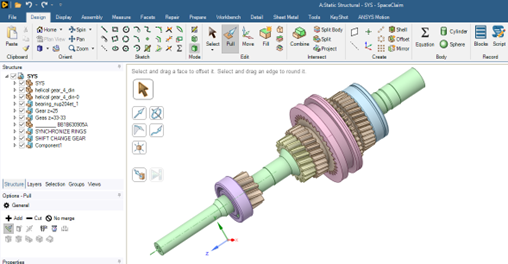
Still intimidated by the new look? Discovery has a plethora of online training materials, as well as tutorials and documentation baked into the application so you can spend less time learning a new interface and more time getting work done. You can also check out DRD’s Discovery learning page for more information.
Ok, Ok, But is Discovery Modeling actually better than SpaceClaim?
So far we’ve covered that Discovery Modeling is highly accessible to existing SpaceClaim users, but is it actually better? We could spend all day discussing the various reasons people are switching to Discovery Modeling, but here are a few of the highlights:
1) Advanced Geometry Cleanup
Clean up models faster in Discovery Modeling with more built in repair and detection features.
2) Advanced Model Prep
Create Beam connections for bolted connections with ease. Model pretension directly in the Discovery GUI, or transfer the connections to Mechanical for higher fidelity solutions.
3) Sub-D
Whether you’re working with 3D scans or geometry generated by Discovery’s topology optimization tool, Designers can say goodbye to STL manipulation headaches with the all new Sub-D modeling. This feature enables interactive organic editing you’ll have to see to believe.
4) Simulation that Just Works
Unlike SpaceClaim, the Discovery GUI goes beyond being just an advanced geometry preprocessing tool by giving designers access to easy-to-use simulation across multiple physics (if Discovery Simulation is licensed). Discovery’s GPU based solvers provide immediate feedback on geometry changes in real time. Need higher fidelity? You can even submit simulations to the flagship Fluent or Mechanical solvers without leaving the Discovery environment.
If you have questions about transitioning from SpaceClaim to Discovery Modeling, one of our experienced staff would love to chat. Contact DRD today to see if Discovery is right for your team!