What are the Licensing Requirements for Ansys GPU Solvers?
How does Ansys licensing work with GPU solvers and cards?
Ansys continues to develop GPU solvers as GPU based computing continues to reach maturity and shows promise as a more efficient and economical way to access powerful high-performance computing. DRD’s benchmarks show significant promise in using GPUs for computational fluid dynamics (CFD) using Fluent’s new native GPU solver and for discrete element modeling (DEM) using Ansys Rocky.
When investigating the use of GPUs to solve your complex and large problems it is important to understand the licensing implications. In this article we will discuss licensing for both Fluent and Rocky when using GPUs.
Fluent requires a CFD Enterprise license to enable the Native GPU Solver. Included in the license is the ability to use up to 40 streaming multiprocessors (SMs) on a GPU with the ability to solve on a card with a greater number of SMs by checking out HPC Workgroup or HPC Pack licenses. The table below shows the required number of HPC Workgroup tasks or HPC Packs required for a given SM count. In some sense the licensing scheme is similar to the CPU solver where HPC licensing is required to solve on more than 4 cores. Similarly, a core is a subset of the compute elements on a CPU die just like an SM is a subset of the repeating compute units on a GPU. It is important to note that an SM is not equivalent to a CUDA core. SMs contain multiple CUDA cores. This article explains how to determine the number of SMs on a given card below. It is also important to know that you must use all of the SMs on a given GPU. You cannot utilize only a portion of the SMs.
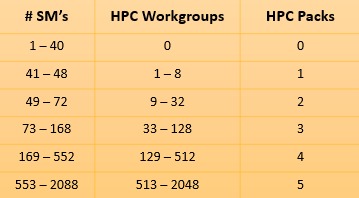
Rocky allows the use of GPUs right out of the gate with up to 112 SMs. Rocky does use it’s own HPC licensing that enables an additional 112 SMs per Rocky HPC 8 License as shown in the table below.
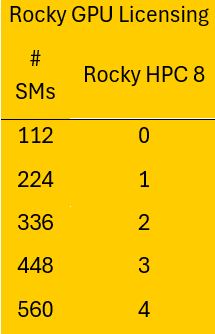
How Many Streaming Multiprocessors (SMs) Are on my GPU Card?
When determining how much HPC is required for a given GPU it is important to know both the target application (Fluent or Rocky) as well as the number of SMs on the card. Since you must consume all of the SMs on the card, you must have sufficient licensing to be able to invoke either solver on the card. The number of SMs on a card is rarely published, so it can seem daunting at first, but DRD has found that the website techpowerup.com readily posts the SM count.
Search for the GPU name and “specs” in google and follow the tech powerup link:
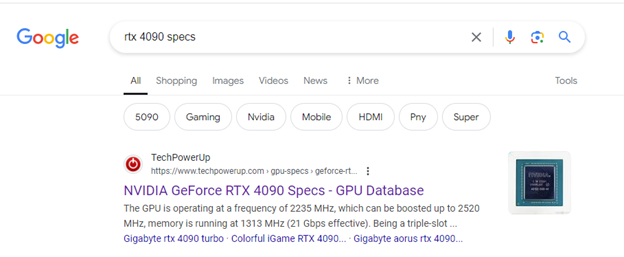
Scrolling down to the details of the card, the SM count is listed in the “Render Config” section:
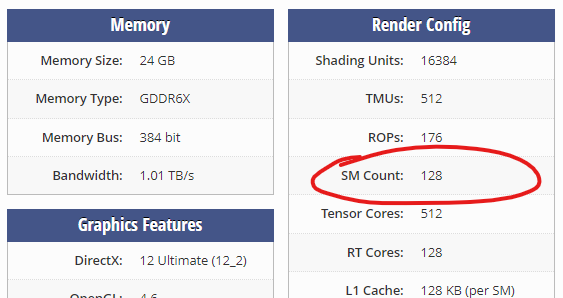
From this example, we can see that to run the Fluent native GPU solver on the RTX 4090 would require 3 HPC packs and to run Rocky on this card would require a single Rocky HPC 8 license.
DRD hopes this article helps answer questions regarding licensing of our world class GPU solvers as well as where to find published streaming multiprocessor counts for modern GPUs. Do you want to see more Ansys GPU benchmarks? Visit our hardware page.