How to Choose the Right Optical Tool: Ansys Speos vs. Lumerical vs. Zemax
Introduction
From the smartphone in your pocket to satellites orbiting Earth, optics and photonics are transforming the way we live, communicate, and innovate. As devices become increasingly complex—combining nano- to micro-scale components, selecting the right optical simulation software is critical.
Ansys offers three powerful and complementary tools in its optics portfolio: SPEOS, Lumerical, and Zemax. While they all serve the optical design space, each is built for different levels of simulation, from chip to system to human perception. Understanding their differences will help ensure your team is using the most effective solution for your goals.
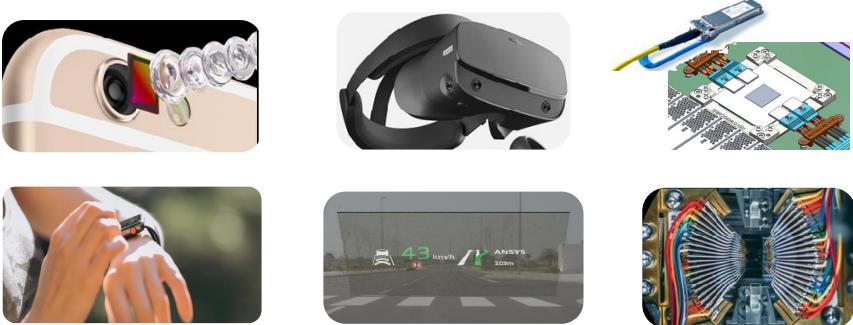
Ansys SPEOS: Real-World Light Simulation
Primary Focus: 3D lighting systems, human vision, and environmental interaction.
Best For: Engineers designing lighting systems, sensors, and displays that need to function correctly in real-world conditions.
Why Use It:
- Simulates how light behaves in real environments.
- Evaluates visibility, glare, and human eye perception.
- Ensures compliance with industry regulations (e.g., automotive lighting).
- Perfect for full 3D scene analysis, including camera and sensor packaging.
Example Use Case: Ensuring a car’s heads-up display (HUD) remains legible in all lighting conditions or verifying that a drone’s sensor accurately interprets glare in outdoor environments. Join our upcoming webinar on Camera Development to explore how SPEOS supports vision analysis in real-world environments.
Ansys Lumerical: Photonics at the Nanoscale
Primary Focus: Photonic components, integrated circuits (PICs), and light-matter interaction at the nanoscale.
Best For: Designers of photonic communication systems, metamaterials, or CMOS sensors.
Why Use It:
- Multiphysics solvers for electromagnetic, thermal, and electronic effects.
- Models waveguides, gratings, quantum devices, and more.
- Ideal for datacom, optical interconnects, and pixel-level design.
- Enables chip-to-system simulations with full interoperability.
Example Use Case: Developing a photonic integrated circuit (PIC) for high-speed optical data transmission in datacenter equipment or optimizing nanostructures on an OLED display. Join our upcoming webinar to learn about chip-level simulation, packaging, and thermal performance.
Ansys Zemax: Precision Optical System Design
Primary Focus: Imaging systems, lens design, and optical tolerancing.
Best For: Optical engineers building AR/VR systems, microscopes, telescopes, or consumer electronics lenses.
Why Use It:
- Combines sequential and non-sequential ray tracing in one UI.
- Offers comprehensive tolerancing and STOP (Structural, Thermal, Optical Performance) analysis.
- Integrates optical and mechanical design, reducing cross-team errors.
- Allows for precise manufacturability assessments from concept to production.
Example Use Case: Designing and optimizing the optical path of a VR headset lens, accounting for structural and thermal effects on image quality. Register for our camera development webinar to see how Zemax enhances lens and optical path design.
How They Compare
Feature | SPEOS | Lumerical | Zemax |
Primary Simulation Type | Light in real-world scenes | Electromagnetic fields (wave optics) | Imaging and lens systems |
Key Focus | Illumination, sensors, vision | Photonic ICs, nanostructures, optical chips | Lens design, tolerancing, STOP analysis |
Industry Use Cases | Automotive, aerospace, consumer devices | Semiconductors, datacom, quantum tech | Medical optics, consumer electronics, defense |
Integration Capabilities | CAD tools (CATIA, SolidWorks) | Photonic EDA, circuit tools | FEA tools, CAD, mechanical design environments |
Simulation Scale | Macro/system-level | Nano/device-level | Meso/system-level (lens to system) |
Want to see these tools in action?
Check out our upcoming webinars, including:
- July 8 at 9AM (CDT) – Camera Development: Leveraging Zemax for lens design, Lumerical for image sensor optimization, and SPEOS for vision analysis.
- July 15 at 9AM (CDT) – Human Factors in Lighting Design: Discover how lighting perception and key metrics impact usability and safety.
- July 22 at 9AM (CDT) – Advancing Metalens Design: See simulation workflows using Lumerical and Zemax for next-gen metalens design.