The Motivation and Method to Study Cracks in Structures (Part 1 of 3 in a series on Fracture Mechanics)
Before we jump into the topic at hand, I’d like to introduce myself. My name is Alex Austin, and I am the Structural Team Lead at DRD Technology, an Ansys Channel Partner. I studied Mechanical Engineering at the University of Tulsa, OK, from which I graduated with a BS and MS in Mechanical Engineering a little over a decade ago (woo… it’s already been that long!). My graduate work was in the fatigue and fracture space. My primary area of expertise is structural mechanics; as many engineers may know, this is quite a large field of physics when we look at Ansys simulation capabilities. Fracture mechanics is a small part of that overall field, is relatively new in the world of engineering, and is very complex.
What is Fracture Mechanics?
When engineers evaluate stress in a structure, the common, simple equation that comes to mind is stress = force/area. This equation carries several assumptions: static equilibrium, uniform cross-sectional area, uniaxial stress, to name a few. With the introduction of a crack to the structure, the state of stress at the crack tip is not uniaxial. Cracks are sharp corners, or notches. In the computer simulation (finite element) world, we call these singularities. In fact, singularities are locations where the theoretical stress is infinite. A strength of materials approach does not account for these singularities. When a crack exists, we need a method to analyze it. Fracture mechanics is that method. Fracture mechanics is the study of crack propagation in materials.
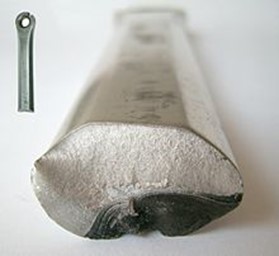
Image Source: Wikipedia
Motivation for Fracture Mechanics
Often, cracks naturally form during the manufacturing process, either through casting or machining methods. Cracks can exist in a product and never cause issues with the working of the structure. In fact, cracks may be invisible to the naked eye. However, when this is not the case, what happens?
Let’s say we’ve designed and manufactured structure that is currently out in the field, and our customer notices a crack… is this a problem? Let’s say a customer reported cracks popping up on some rotating machinery housings and they simply asked, ‘Is this a problem?’ though, the more likely case is no questions and, ‘Please fix this!!!’. What is the engineer typically tasked with determining? The common questions we ask are:
- Will the crack grow? If so,
- How quickly will the crack grow? And then,
- Will the structure fail catastrophically?
As stated, the customer absolutely thinks the presence of a crack is a problem. This is commonly the case when the customer is not an engineer, and even if they’re an engineer, they had no insight into the design and manufacture of the product. Answering the above questions will directly determine if the crack is or is not a problem.
What about the case where the engineer designs a structure and during the design process must consider a structure that has cracks? This is a common practice in regulatory bodies, namely, the FAA (Federal Aviation Administration). In this case, the engineer assumes a crack or cracks exist in the designed components and must design for this potential failure mode. This is referred to as Fatigue and Damage Tolerance. The engineer establishes inspection intervals for components based on this analysis. The maintenance crew knows how many hours the component can be used before it needs to be checked for integrity and possibly replaced.
In the next blog post, we will discuss the methods to evaluate cracked structures.