Why is Ansys Rocky a Must-Have for Engineers?
Introduction
In the fast-paced world of engineering simulations, Ansys Rocky stands out as a game-changer for particle dynamics. Whether you’re working in mining, pharmaceuticals, agriculture, or any industry that deals with bulk materials, Ansys Rocky provides unmatched accuracy, speed, and scalability in Discrete Element Method (DEM) simulations.
As industries push the boundaries of digital engineering, integrating Ansys Rocky with CFD (Computational Fluid Dynamics), FEA (Finite Element Analysis), and Multiphysics solutions ensures a comprehensive approach to real-world problem-solving. In this blog, we’ll explore how Ansys Rocky is reshaping engineering design and how you can leverage it for optimized results.
What Makes Ansys Rocky Stand Out?
1. Advanced Particle Shapes and Breakage Modeling
Unlike traditional DEM tools that rely on spherical approximations, Ansys Rocky allows for realistic particle shapes, including clusters, fibers, and shells. This results in highly accurate predictions of bulk material behavior, leading to more reliable product designs and operational insights.
2. Seamless Multiphysics Integration
By integrating with Ansys Fluent and Ansys Mechanical, Ansys Rocky enables users to study:
- Fluid-particle interactions (ideal for industries like pharmaceuticals and food processing)
- Structural loads due to bulk materials (important in conveyor and mining applications)
- Thermal effects on particle flow This synergy provides engineers with a holistic understanding of how materials behave under various conditions.
3. GPU Acceleration for Faster Simulations
Time is money, and Ansys Rocky ensures maximum efficiency with its GPU-accelerated solver. Users experience up to 50x faster computation speeds compared to traditional CPU-based solvers, significantly reducing simulation time and enabling rapid design iterations.
4. Realistic Conveyor and Comminution Analysis
For industries dealing with bulk material transport, Ansys Rocky provides detailed conveyor belt wear analysis and crusher/grinder efficiency predictions. These insights help manufacturers optimize equipment lifespan, reduce downtime, and improve overall productivity.
Our exclusive webinar will walk through real-world case studies, demonstrate simulation workflows, and show how Rocky integrates with other Ansys tools effectively.
Industry Applications
1. Mining and Material Handling
- Predict and mitigate conveyor belt wear and tear
- Optimize grinding and crushing efficiency
- Reduce maintenance costs and improve operational reliability
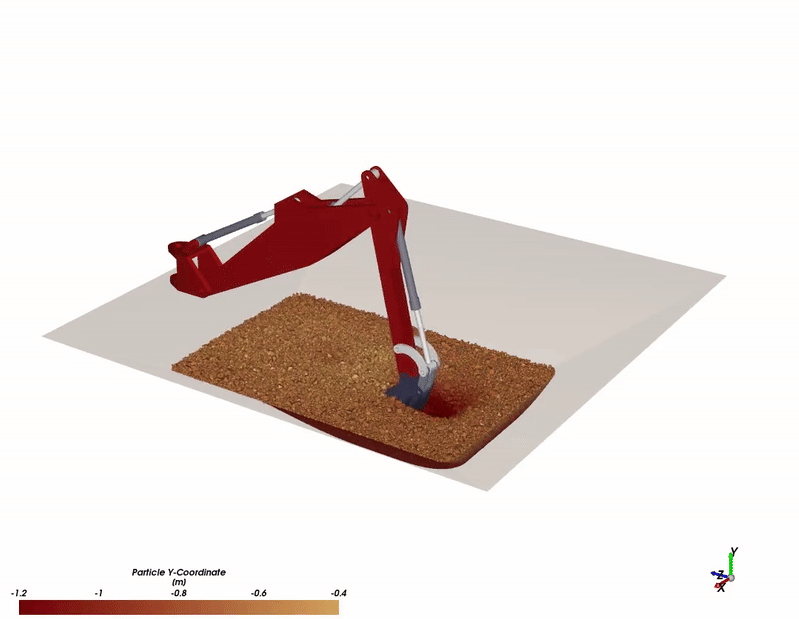
2. Pharmaceuticals and Food Processing
- Model tablet coating and powder mixing
- Improve granulation and capsule filling processes
- Enhance product uniformity and reduce waste
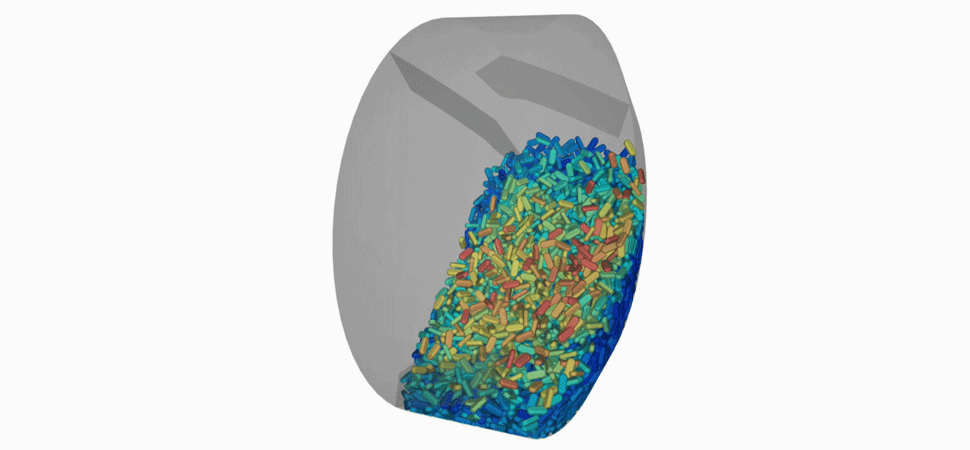
3. Agriculture and Fertilizer Production
- Simulate grain flow and storage behavior
- Optimize fertilizer blending and application processes
- Reduce handling losses and ensure product consistence
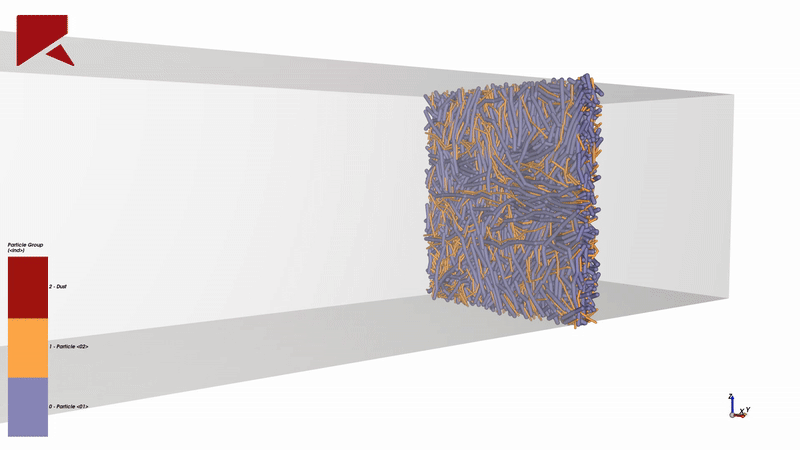
How to Get Started with Ansys Rocky
Step 1: Define Your Simulation Objectives
Identify what you want to achieve—whether it’s reducing equipment wear, optimizing material flow, or improving product consistency.
Step 2: Import and Set Up Geometry
Ansys Rocky allows direct CAD imports, making it easy to create accurate simulations with real-world geometries.
Step 3: Select the Right Particle Model
Choose from a variety of particle shapes and material properties to best represent your system.
Step 4: Run GPU-Accelerated Simulations
Leverage parallel processing for faster and more detailed results.
Step 5: Analyze and Optimize
Use Ansys Rocky’s visualization tools to interpret results and refine designs for maximum efficiency.
Conclusion: Why Ansys Rocky is a Must-Have for Engineers
Ansys Rocky is more than just a DEM tool—it’s a simulation powerhouse that bridges the gap between physics-based modeling and real-world applications. With advanced particle modeling, seamless multiphysics integration, and high-speed processing, it is a must-have solution for industries looking to innovate and optimize their bulk material handling processes.
If you’re ready to take your simulations to the next level, contact us today for a demo or trial of Ansys Rocky and see how it can transform your engineering workflow! Our upcoming webinar showcases the advanced simulation tool designed for modeling granular and discontinuous materials across industries like pharmaceuticals, mining, food processing, and manufacturing.