Introduction
In the ever-evolving world of product development for all kinds of industries including aviation, automotive, manufacturing, and healthcare, engineers face many challenges while developing a final product that meets requirements. Both physical prototyping and software simulation help engineers model and analyze different systems, processes, and products. Understanding the differences between these two methods becomes crucial for developing products on-time and on-spec. In this blog, we’ll explore the distinctions between traditional prototyping and software simulation to help you choose the right path for your project.
Physical Prototyping
The setup and integrations required for physical prototyping consists of having design software, materials, test equipment and techniques, and quality assurance. The materials will vary depending on the nature of the project but can include raw materials, electronic components, or mechanical parts. Having the proper equipment also requires the right safety equipment to ensure a safe working environment.
Software Simulation
The setup and integrations required for software simulations depend on a few common elements and considerations. Hardware must be capable of running the simulation software with sufficient processing power and memory, and software should be selected based on specific features for your simulation. Lastly, training and support materials for users and developers are helpful for long-term success.
Both software simulation and physical prototyping have a place in the product development cycle. These two approaches serve different but complementary purposes within the product development process. Engineers must determine how much physical testing can be avoided through the use of software simulation during product development. With the understanding of cost, time, and product requirements, they can choose the best path to ensure that the final product meets the desired specifications and quality standards.
Cost Considerations Drive Decisions
Software simulation may result in a higher initial investment in terms of software and training. These upfront costs are associated with developing or implementing a simulation software system for a specific purpose. Many simulation products come with licensing or subscription fees that can be one-time, monthly, or an annual renewal cost. However, software simulations generally have a lower long-term cost and reduce the need for physical materials, machinery, and labor that are necessary for physical testing. For applications where upfront cost is the absolute deciding factor, physical prototyping can be the right solution. For organizations looking to invest in their product development cycle, simulation provides a long-term solution that can be used repeatedly as you modify and evolve a product or create new products.
Speed
Time to market is a critical factor for many projects across all industries. It is based on the scope and complexity of the project, the team’s experience with software, and access to all resources required to complete the project. Simulation provides a digital platform that invites collaboration for sharing, analyzing, and discussions. It is more accessible to work collaboratively across distances saving time than requiring physical presence, which can create logistical challenges.
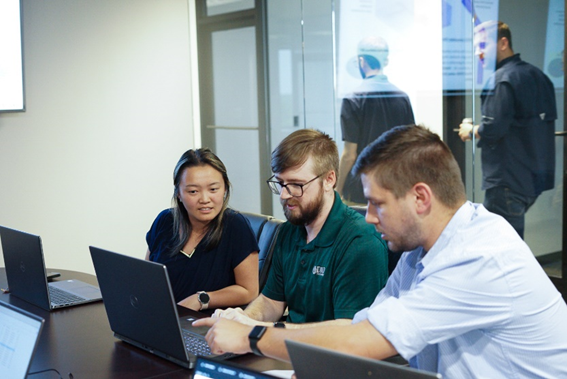
Risk assessments are paramount in product development. Simulation can help identify potential risks and issues early in the process, saving time and resources. The common risks and challenges associated with simulation varies from the quality of data input, the possibility of bugs or limitations in software tools to produce inaccurate results, and ensuring the model accurately fits the real-world representation. When time is not a critical factor for projects, physical prototyping is often used in product development. One would have the ability to physically interact with the product quickly, giving you a real-world sense of its form, function, and usability. Simulation abates the need for physical components – when supply chain constraints are an issue, engineers using simulation can begin testing based on the software-defined version of their product rather than having to wait for physical prototypes.
End Product Variables
Building physical prototypes can be expensive if numerous iterations are required. Several types of products and industries often involve more than one iteration due to the complexity and need for optimization. In the electronics industry, products like smartphones and laptops undergo frequent iteration to incorporate the latest improvement and enhance user experience. In the Aerospace industry, complex systems like aircraft and satellites require extensive iterations to meet the strict guidelines. Car manufacturers and development of medical devices to name a few more.
Software simulation allows for rapid testing and iterations as many changes can be made virtually with a few clicks. This allows for quick changes and adjustments without the need to rebuild physical models. The flexibility to develop multiple iterations saves both time and resources. In contrast, physical prototyping may require more time and resources through each iteration. While physical prototyping for real-world testing is a crucial phase in product development, ideally it would be limited due to the time and costs involved. In addition, during real-world testing, unexpected issues or challenges can arise that are native only to the test environment.
Nelson Global harnessed the power of software simulation in this real-world example to optimize their muffler designs for refrigerated transport vehicles. By leveraging simulation, Nelson Global significantly reduced development time and costs, all while enhancing efficiency, reducing emissions, and meeting regulatory requirements. Nelson Global used the Ansys software suite to design two mufflers within three days. The typical duration for physical prototyping would be weeks involving manual hand calculations with less of an accurate outcome.
In the end, both software simulation and physical prototyping have their places in product development. For many, a combination of both approaches can be the most effective solution. Starting with software simulation for the initial design and risk assessment, and then transitioning to physical prototyping for real-world testing. The right approach is the one that will align with your project’s requirements.
The combination of Ansys, a globally recognized simulation tool, and DRD Technology, an integrator for Ansys tools, offer a comprehensive approach to product design and optimization. Ansys provides a suite of engineering simulation software tools that are widely used in various industries to simulate real-world scenarios. Ansys software simulation includes but is not limited to structures, fluid dynamics, electromagnetics, optical simulation, acoustic, and thermal analysis. These tools can be used in a wide range of industries including aerospace, automotive, electronics, manufacturing, and many more. Ansys Elite Channel Partner, DRD Technology, has achieved the highest level of proficiency and met rigorous performance requirements with the Ansys platform so that we can help you design, simulate, and succeed.
To learn more, read the full case study documenting how Nelson Global took their prototyping process from weeks to just three days using simulation.